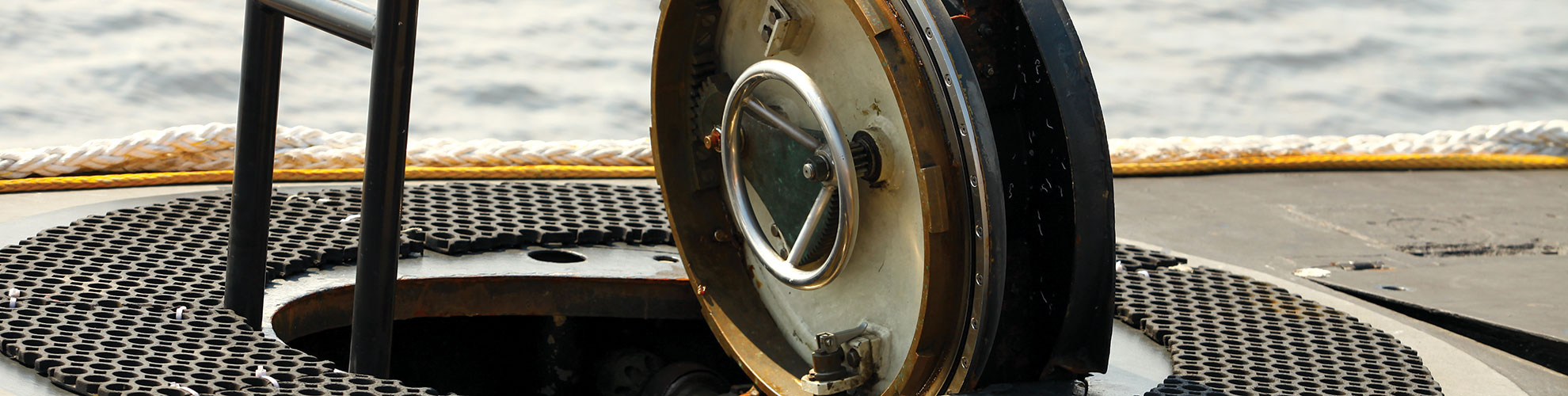
Marine Grease®
Submarine hanger areas have actuated parts, doors, hatches, etc., that must be adequately lubricated to function correctly and extend service life. Dry deck shelter hatches need lubrication on all internal gears and locking ring threads. Texas Research Institute Austin, Inc. (TRI Austin) has developed an innovative grease approach utilizing fluorohydrocarbon base oil in conjunction with a thixotropic filler and various anti-corrosion additives.
This diver-safe optimized formulation has performed very well in both field and lab testing. It is resistant to water washout, prevents corrosion both actively and passively, and has passed the NAVSEA P-9290 certification for off-gassing of volatile compounds. The new grease can be applied by hand, grease gun, or via grease lines. Reduced costs will be realized with the new grease through improved durability, reduced need for component repair, and minimal application time.
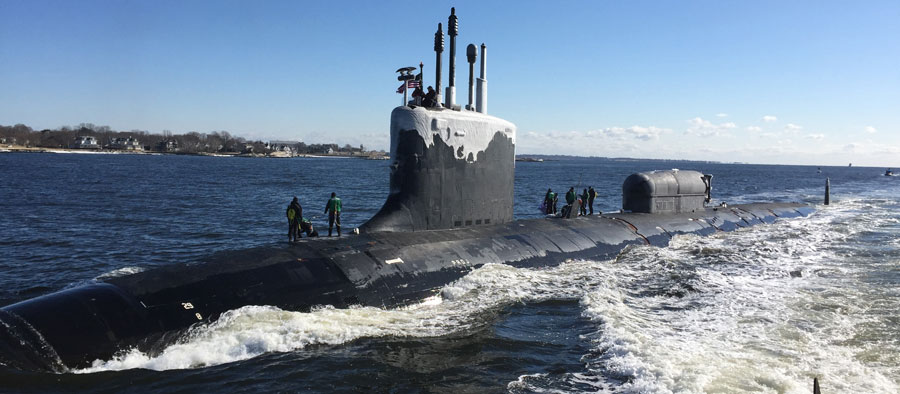
Material Specification and Qualification Testing
Marine Grease® provides:
• Resistant to washout
• Prevents corrosion
• Non off-gassing
• Improved durability
• Reduces repair costs
• Reduced application times
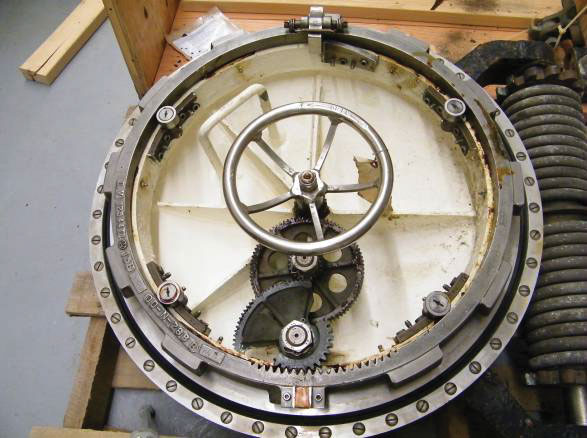
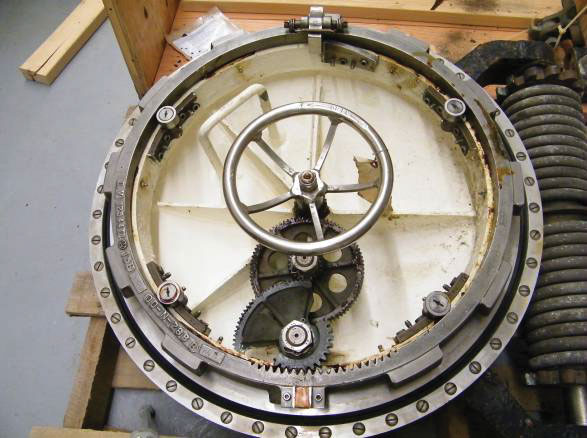
STANDARD TEST METHOD | TEST | PURPOSE OF TEST | TEST RESULTS |
---|---|---|---|
ASTM-D-1403 | Small Scale Cone Penetration | ¼ Scale Penetration, Unworked and Worked | Unworked – 244 Worked – 254 |
ASTM-D-2595 | Evaporation Loss @ 22 hours | Measurement of permanence | 0.70% |
ASTM-D-942 | Pressure Vessel Oxidation @ 100 hours | Measure the net change in pressure resulting from consumption of oxygen by oxidation and gain in pressure due to formation of volatile oxidation by-products | 2.0 psi drop |
ASTM-D-2266 | Four Ball Wear of Grease | Used to determine the relative wear preventing properties of greases under the test conditions | 0.56 mm |
ASTM-D-2596 | Load Wear Index of Grease | Determination of the load-carrying properties of lubricating greases | 95.71 |
ASTM-D-1478 | Low Temperature Torque | Determination of the starting and running torques at low temperatures (below -20°C (0°F)) | Starting Torque 9024 g-cm 1 Hr Running Torque 732 g-cm |
FTM-5309 | Copper Corrosion of Grease | Detection of Copper Corrosion from Petroleum Products by the Copper Strip Tarnish Test | Exposed 3B Immersed 4A |
FTM-321 | Oil Separation | Wire Cone Method | 4.21% |
FTM-5415 | Resistance of Grease to Aqueous Solutions | 1 week exposed to water and water/ethanol | 0% disintegration |
FTM-3005 | Dirt Count of Greases | The number of foreign particles between 25 and 75 microns per milliliter of sample, and particles greater than 75 microns per milliliter of sample | 25 - 74 µ – 38/cc +75 µ – 0/cc |
ASTM G72 | Autogenous Ignition Temperature in Oxygen-Enriched Environment | To establish the average autogenous ignition temperature (AIT) in a 99.5% mol O2 environment. | 247oC +/- 4oC |
ASTM D4809 | Heat of Combustion of Liquid Hydrocarbon Fuels by Bomb Calorimeter | To establish the average heat of combustion in a sealed enironment with an ignition source. | 2,003 +/- 9cal/g |
ASTM D2515 | Test Material with Liquid Oxygen Impact Sensativity Threshold (Pass-Fail Techniques) | To establish the the liquid oxygen (LOX) impact senativity to material degradation over 20 test runs. | Passed all 20 test runs with no LOX reactivity |
ASTM G74 | Test Material for Ignition Sensativity of Nonmetallic Materials and Components by Gaseous Fluid Impact | To establish the material’s 50% reaction pressure for gaseous fluid impact sensativity (GFIS) over a varying range of pressures (290psig-1450psig). | 50% reaction pressure is 635 psig |
ASTM G125 | Test Material for Measuring Liquid and Solid Material Fire Limits in Gaseous Oxidants | To establish the minimum percent O2 index (OI) threshold for the material to ignite with a secondary source and burn. | No Burn Threshold is 37% O2 |