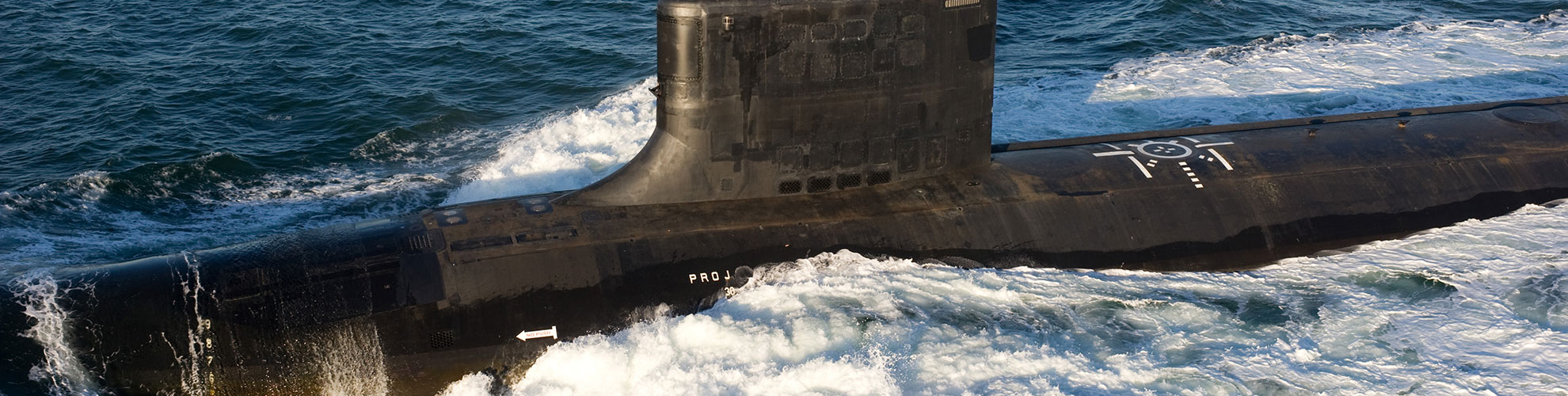
Bond-Coat™
Bond-Coat™ is a multi-layer plasma-applied coating system created to improve rubber-to-metal long-term adhesive bond strength and prevent cathodic delamination. It is intended for application on industrial and marine hardware exposed to severe environments involving high pressure, extreme temperatures, chemical exposure and cathodic delamination issues.
Tests performed by the U.S. Navy compare standard overmolded backshells and backshells treated with Bond-Coat™. Both were subjected to a variety of saltwater conditions, pressure changes and temperature swings. The results demonstrated Bond-Coat’s™ improved bonding strength in harsh environments, superior protection against cathodic delamination and its ability to work with all metal substrates and existing molds. The Navy results also show superior service life in accelerated life testing and in service use by up to 5X over standard overmolded parts exposed to similar environments.
Bond-Coat™ required by the U.S. Navy
The U.S. Navy sought help from Texas Research Institute Austin, Inc. (TRI Austin) with a chronic problem: the failure of underwater electrical connectors on submarines. The problem was cathodic delamination, which caused underwater cable connectors to fail prematurely, sometimes in two to three years due to dissimilar metal coupling and ensuing electrolytic reaction.
In response, TRI Austin created Bond-Coat™. Applied to the connector back shell,
Bond-Coat™ prevented cathodic delamination and extended connector life by 200%. Plus, it saved the Navy $814,400 per submarine over the life of the connectors, even before considering savings due to improved combat readiness. The federal government now requires Bond-Coat™ on Navy underwater connectors and other outboard equipment.
Use of Bond-Coat™
On any metal surface prior to elastomer bonding or encapsulation. Alcohol wipe is the only surface preparation needed. All metal substrates can be coated: stainless steel, Monel, titanium and aluminum-silicon bronze.
Bond-Coat™
Advantages
- Stops cathodic delamination
- Increases initial bond strength
- Removes need for toxic primer systems
- Enhances bond longevity
Applications
- Underwater connectors
- Downhole assemblies
- Transducer housings
- Marine sensor applications
- Any critical rubber-to-metal bond
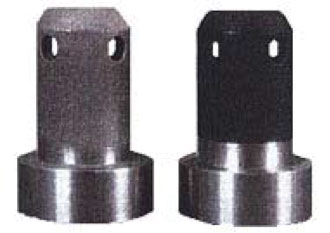
- Creates bonds that survive harsh environments (high pressures, high temperatures, chemical exposure, electrolysis)
- Increases the bond strength of exotic materials such as Viton®, Neoprene and polyurethane
- Non-conductive, eliminating cathodic delamination/corrosion due to chemical or moisture penetration
- Works with existing molds
- Part can be anodized after application of Bond-Coat™
- Ideal for all metallic substrates, including Inconel, titanium and aluminum
Improves bond strength for longer life
Bond-Coat™ significantly outperforms standard rubber to metal bonds exposed to harsh environmental conditions. It’s the perfect protection for bonded materials in high-pressure, extreme temperature environments, such as downhole assemblies, transducer housings and marine sensor packages – any application where corrosion, debonding and peeling are a problem.
Eliminates cathodic delamination
Because Bond-Coat™ is non-conductive, it is impervious to cathodic delamination, a primary cause of adhesive primer deterioration in marine environments.
Use with existing processes
Bond-Coat™ can be selectively applied to discrete areas of a part to be over-molded, leaving other surfaces unaffected. As a result, existing connector molds do not have to be altered. Aluminum hardware can also be anodized after applying the Bond-Coat™ providing a seamless interface between the Bond-Coat™ and the anodized area.
Superior molding properties for metals and polymers
Use Bond-Coat™ with all metal substrates, including stainless steel, monel, inconel titanium, aluminum and aluminum-silicon bronze. It even increases the bond strength of many standard elastomers, such as Neoprene, polyurethane and some Vitons.
About TRI Austin, Inc.
TRI Austin was founded in 1975 to address reliability and materials needs of the US Navy, and advanced materials and technologies for the Department of Defense, NASA, and other Government and Commercial clients. We have evolved into an organization that provides engineering services and advanced material development for global clientele while based in Austin, Texas.
We have developed a variety of innovations that are now commercially available, including protective coatings for electrical connectors, an environmentally friendly
lead substitute, and a new aircraft adhesive.